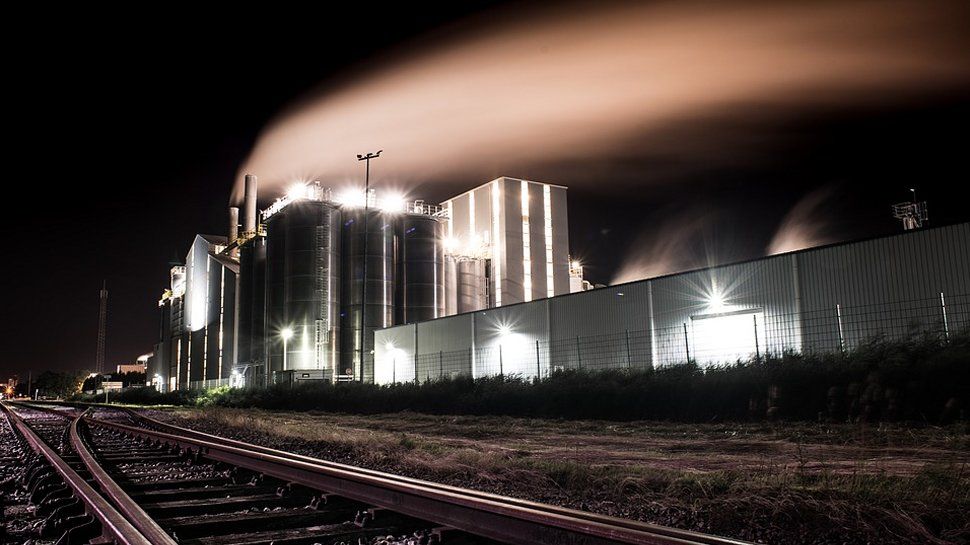
The last twenty years have seen more warehousing and logistics transformations than ever before. In this relatively short period of time, warehouse operators have taken a closer look at how they can get more visibility into their operations by increasing the level of digitization – not only in their own locations but also when collaborating with their supply chain partners. Decades-old technologies such as warehouse management systems (WMS), barcoding and data analytics, have played a key role in making this happen. Today, warehouse modernization starts with focusing on workers and workflow optimization, then adopting new technologies to integrate and synchronize with existing WMS and automation, as well as thinking ahead to future investments.
The evolution of warehousing, distribution, fulfilment and logistics continues rapidly. As we review the top technology trends, it’s important to keep in mind that warehouse operators need to future-proof their investments today to lay a solid foundation to adopt these new tools and place themselves in a strategic position. According to a recent Warehousing Vision Study, 61% of warehouse operators said they will augment people with technologies, and more than three-quarters (77%) of decision makers agree that they need to modernize operations across the warehouse to remain competitive in the on-demand economy.
Managing critical information
Critical information can be managed in real time with radio-frequency identification (RFID) tracking, locating systems and temperature sensors. When an enterprise has constant visibility into its warehouse systems, a wealth of data insights and new efficiencies are derived. Thanks to sensor technology, warehouse managers are continually tracking their asset attributes such as location, contents, physical condition and dwell time.
Equipping the physical environment can happen in phases. Start with identifying critical areas that need full operational visibility such as fixed RFID ports in one or two dock doors, 3D sensors inside a trailer or real-time locating solutions (RTLS) within an entire receiving or shipping dock. Warehouse managers can also choose to implement real-time sensing technology in their wall-to-wall operations. With Bluetooth® Low Energy (BLE) beacons, proximity events are reported and enforced, contact tracing keeps employees safe and outbound shipments get verified automatically. Another option is Ultra-wideband (UWB), a short-range, wireless communication protocol designed for applications requiring a high degree of accuracy to track high-value assets. With greater integration into warehouse management and execution systems, these will continue to provide warehouses of the future with essential capabilities.
System of reality
These technologies provide a digital view of physical operations and create a “system of reality” that allows warehouse operators to capture and manage critical information across their warehouse and logistical operations. Their benefits include:
- Maximizing visibility into warehouse assets
- Improving inventory management
- Making locating items easier and faster
- Increasing throughput and alert for risks in the supply chain, as well as manage by exception
- Complying with chain-of-custody regulations
- Reducing damages and loss to shipments and assets
RFID and RTLS solutions combined with temperature sensors enable warehouse operations to closely monitor the real-time temperatures of vaccines, pharmaceuticals, food, and other perishable items. These sensors also alert workers when temperature thresholds are reached, ensuring that sensitive goods arrive at their destination without ever having been compromised. Demand for this type of robust, real-time monitoring, along with blockchain services, will increase in the coming years to help ensure the health and safety of consumers.
Help workers complete tasks with augmented reality
Mobile devices already play a key role in today’s modern warehouse. Laptops, tablets and scanners accelerate workflows, enable locating through BLE, connect workers and gather transactional data for reporting and actionable insights for improvements.
The latest innovations combine mobility with augmented reality (AR) to elevate warehousing efficiency levels. AR layers artificial intelligence (AI) over physical reality so that workers can reap the benefits of both. Imagine walking down a warehouse aisle wearing an enterprise heads-up display with an AR application. On approaching the item’s location, the area lights up with the product’s picture, the quantity to pick and where to place it on the cart. Continuing down the aisle, workers are guided by the application to the remaining items’ locations, which may also display a list of goods, their location and the fastest route through a warehouse to their destination. It can also be superimposed on vehicle windshields such as on forklift trucks for this same function.
Additionally, AR can accelerate onboarding by facilitating training while new employees are at work. It can help improve job safety and efficiency by consistently providing best-practice reminders and other up-to-date information for workers in real time. This enables constantly connected workers with instant communication for better collaboration.
Optimize workflow by combining workers and AMRs
Autonomous mobile robots (AMRs) are gaining popularity in light of resource shortages and high turnover. These robotic solutions can work side-by-side with people, leading to increased productivity by significantly reducing idle and travel time that’s associated with movement of items. This empowers workers to focus on higher-value tasks requiring agile problem-solving to increase customer satisfaction. AMRs help address and reduce high turnover rates by providing opportunities for workers to up-skill in their otherwise-restricted roles. From a management standpoint, they empower warehouse operators to reallocate their workforce for better productivity.
AMRs play an essential role in workflow optimization. For example, an optimized picking operation where multiple orders are prioritized are sent directly to the worker nearest the pick location of those items on their wearable edge device. Just as the last item is picked, an AMR collects the orders and drops off an empty cart of items to be replenished. Without missing a beat, the operator continues to the next task.
As people become harder to recruit and onboarding times become longer, AMRs can complement workers who are already augmented with handheld and/or wearable technology. Training can be expedited and simplified with AMRs empowering operators to work more productively with fewer physical requirements. Three-quarters of respondents to the 2024 Warehousing Vision Study agreed that optimal operational balance in warehousing includes human interaction using either partial automation or worker augmentation.
Improve operations with AI, machine learning and automation
Internet of Things (IoT)-connected devices and data platforms empower robust artificial intelligence (AI), machine learning (ML) and intelligent automation. This creates significant possibilities which is why warehouse decision makers need to understand how AI and ML can boost their operations in relation to their current key performance indicators (KPIs) and vision of the future.
AI can be integrated into warehouse operations in stages with different levels of capital investment over time, without requiring a complete transformation. Keep in mind that modernizing warehouses with the appropriate technologies lays the foundation for future implementations. AI is a driver of automation which is integrated in many warehouse and logistic companies to some degree. The most innovative warehouse operators will deploy these technologies in their infrastructures, supply chains and workflows. Examples of potential developments are:
- Use of self-driving vehicles for shuttle systems within warehouses to automate high-density storage operations
- Increase returns management efficiency by utilizing machine vision for inspections, continually learn patterns for acceptable returned items
- Utilization of AI and automation to streamline warehouse operational workflows for faster put-away and accessibility of high-turnover goods
Achieve wall-to-wall visibility for actionable insights and prescriptive results
Big data may not be new, but it is becoming increasingly sophisticated. With smarter and more secure edge devices such as mobile computers, scanners and printers combined with the widespread use of RTLS, warehouse operators are better equipped to collect data.
But this is only the start. It’s how the data is used that counts. By leveraging AI, ML and applications using application programming interfaces (APIs) powered by enterprise platforms, companies can predict and adapt their workflows in real time based on data from the edge. Warehouse staff can receive data insights plus clear, targeted corrective actions that unlock greater productivity and overall supply chain excellence. Warehouse operations using these technologies are integrating them with existing hardware, software, and data ecosystems to achieve a holistic view of their business. As these data capture capabilities expand, they will be essential for the warehouses of the future.
Next-generation devices and applications are being designed with IoT connectivity, data flow and analytics, considering the increasing need for prescriptive analytics in warehousing. Its benefits include:
- Making smarter forecasts based on real-time market demand shifts and inventory planning trends
- Identifying and mitigating areas of heightened risk as supply chains become larger and more complex
- Adapting faster to supply chain challenges, including delays, supply interruptions, labor shortages and unexpected cost increases
- Managing peak periods more efficiently to maintain availability and sustain unexpected demand surges
- Increasing throughput volume, speed, agility and accuracy across all operational areas
Modernizing warehouses today has never been more vital
Warehouse operators have experienced a lot of disruption and know that modernization is necessary for successful supply chain execution, not only to meet current demands but to set the stage for new innovations. Enhancing their abilities to sense and track their assets, inventories and workflows has never been more critical for warehouse leaders. Most important are the steps of analyzing and acting on the data outputs for informed decision-making and strategic actions that help to optimize operations. The future of technology opens a realm of possibilities—by 2025, this will help create a new era in warehousing.
- Mark Wheeler, Director, Supply Chain Solutions at Zebra Technologies.